In an age where greener work practices and recycling is being brought to the forefront of our collective attention, Derbyshire based swivel joint specialists, Rotaflow, are doing their bit to repair, reuse and recycle wherever possible.
There’s a triple benefit here – first of all there’s a reduction in the amount of perfectly good parts that need to be disposed of, potentially contributing to the rising pressure on landfill sites. Secondly, there’s a much faster turnaround for the customer. Stripping, cleaning and refurbishing parts is typically significantly faster than the design and manufacture of new parts.
This allows a job to be completed quickly, allowing the business to move on to other projects.
The third benefit is cost – Rotaflow always advise if it is not cost effective to repair a swivel joint over the price of a replacement. If it can be refurbished then as a customer you’d always pay less for the job, which allows the savings to be passed down the line.
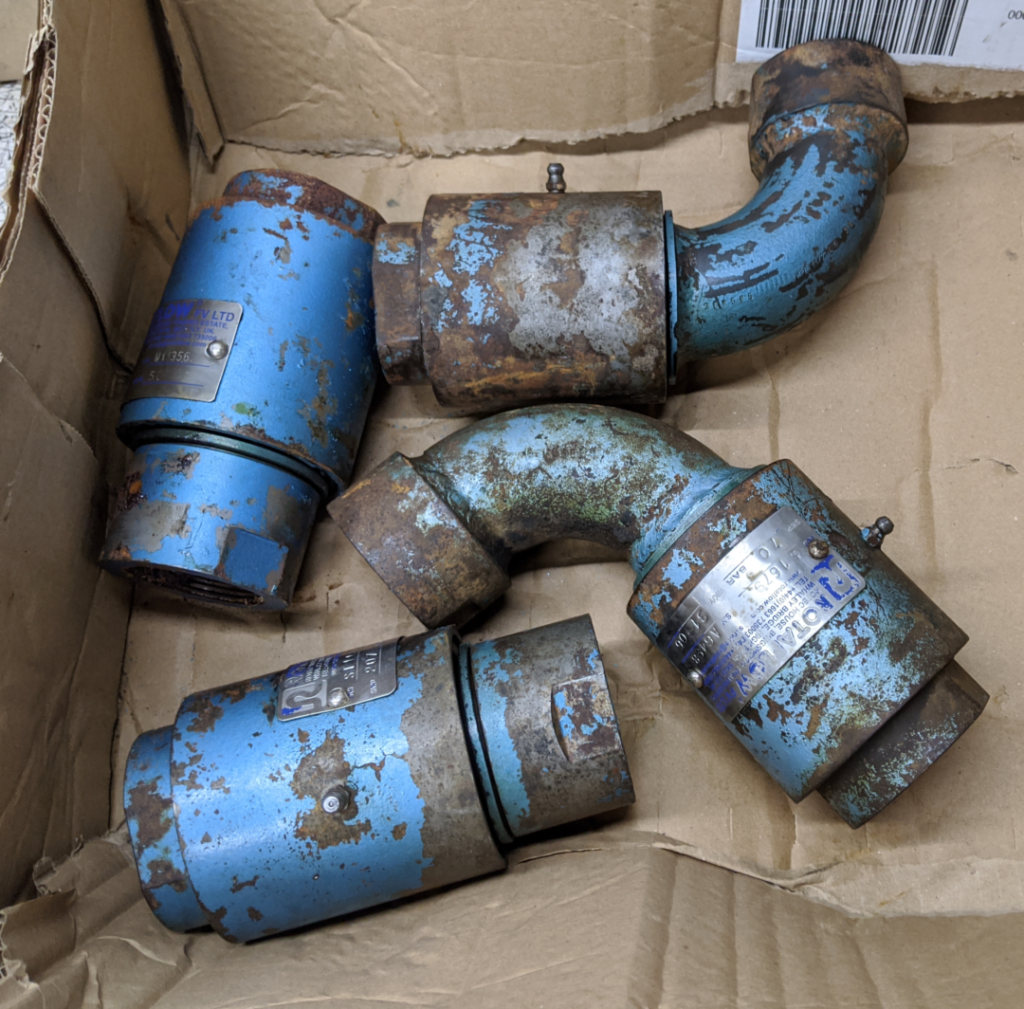
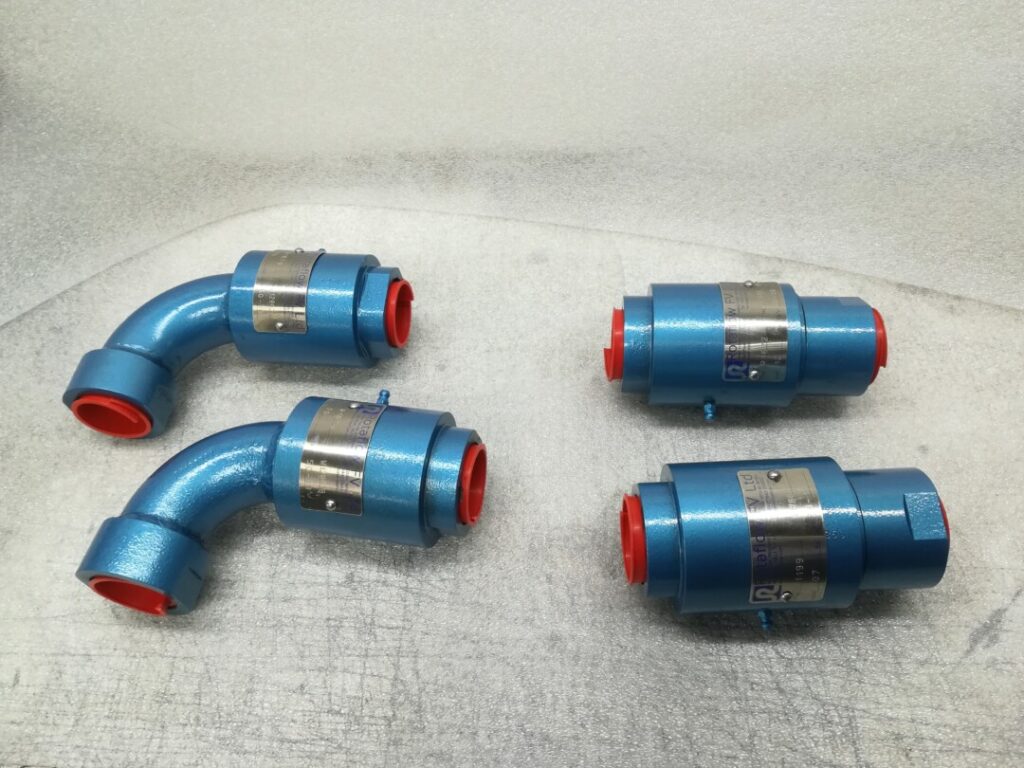
Another, perhaps more subtle benefit is the reputation boost for you as a business. If you’re honest enough to suggest a parts repair and refurbishment rather than a more costly full replacement, you’ll save your customer money and would be more likely to secure repeat business from them in the future.
An Example of Repair and Refurbishment in Practice
Earlier this year Rotaflow completed a full refurbishment of several 6″ nominal bore bespoke swivel joints complete with mounting bracketary and electrical earthing cables. These particular items had seen over a decade of use at a UK based oil and gas refinery.
Each swivel would form part of a loading arm that would transport products to and from ships at the dockside. The joints were worn from the extensive use and long-term exposure to the environment, but the wear wasn’t significant enough to warrant a complete replacement.
A significant number of major components were reused to save both time and cost on refurbishment
The joints were removed from site and sent directly to Rotaflow. Once received they were assessed by experienced engineers before being fully stripped, cleaned and made ready for processing. The joints were re-sealed, fitted with new bearings and pressure tested before being finished in a professional paint specification. This particular specification had been specifically requested by the client for this application.
After the full refurbishment and testing, the swivel joints could be dispatched on a next day service before being refitted back on site, saving the client significant amounts of time and money, not to mention reducing the severity of impact on business. If the swivel joints had to be made from scratch the time delay would have been significantly longer.
What makes this particular job unique is that of the three swivel joints that were refurbished, only two of them were originally designed and manufactured by Rotaflow. The expertise of the Rotaflow engineers enabled them to fully refurbish joints made by other engineering outfits, improving on their specifications and bringing them back to a brand-new standard.
Rotaflow routinely pressure test all of their swivel joints, including refurbished swivel joints, giving piece of mind that your unit will be ready for use. This reassurance is part of the reason major engineering firms trust Rotaflow to work on parts they didn’t manufacture in the first place.
This green approach is something Rotaflow are proud of. Thinking of repairing and refurbishing before new manufacturing has led to a number of jobs being completed in a significantly shorter time frame than usual.
If all more firms use the same approach, perhaps the industry will take a progressive step towards greener practices.
If you have an engineering problem and require specialist solutions, or you have parts you’d like to discuss refurb rather than replacement of, contact us on…
Tel: +44(0) 1663 735003